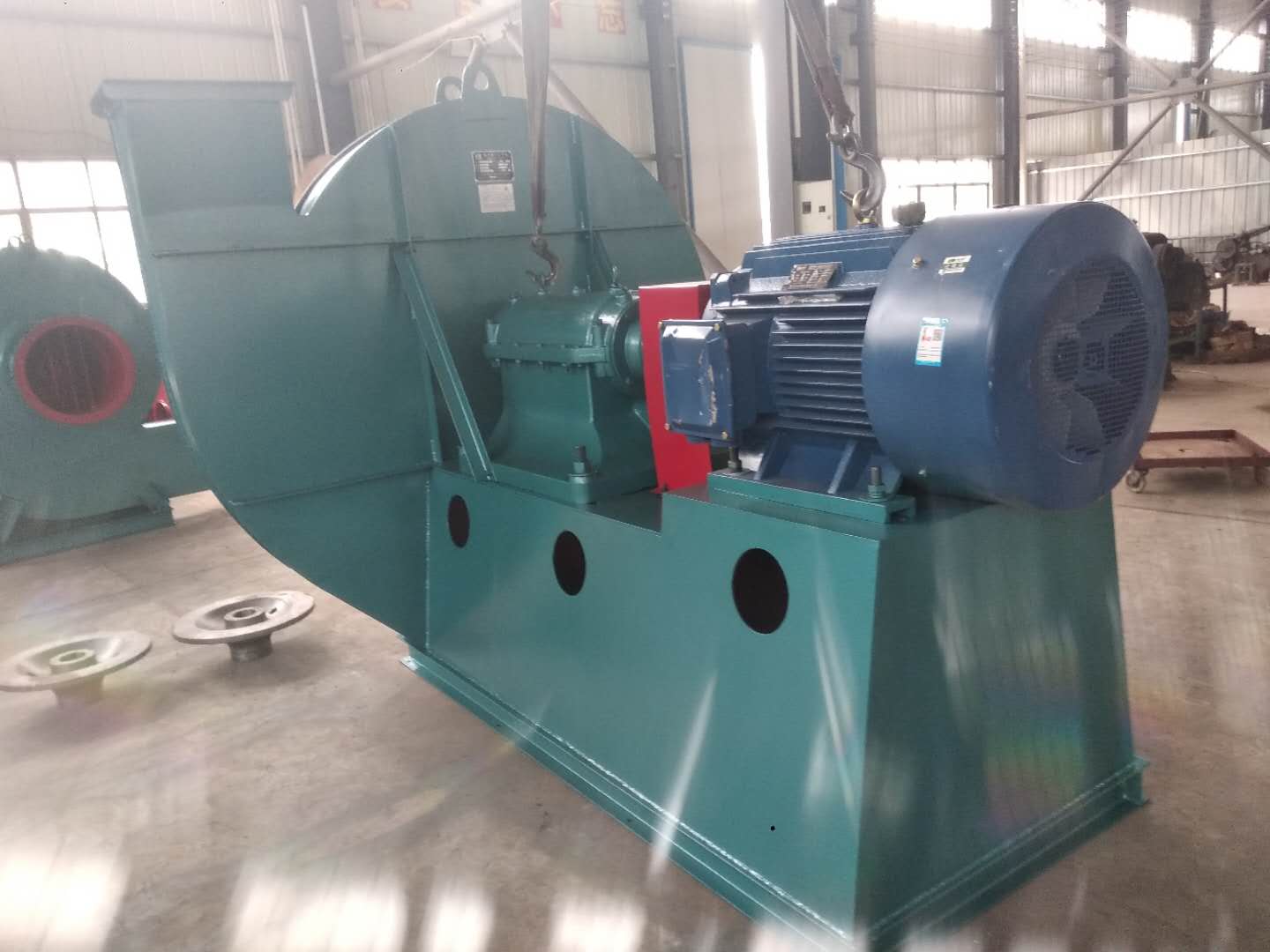
The operating principle of wet electrostatic precipitator is different from other equipment. The dusty gas enters the expanded ash hopper of the wet electrostatic precipitator for pre collection, and is evenly distributed between each filter bag through the guide plate. The dust is retained on the surface of the filter bag. In order to make the equipment resistance not exceed 1200pa, the high-pressure gas will pulse through the electromagnetic pulse valve, so that the compressed air in the air bag will be ejected from the nozzle hole (called primary air) The surrounding air (called secondary air), which is several times of the primary air, is induced through the venturi to enter the filter bag to make the filter bag expand rapidly in an instant, and shake off the dust with the reverse effect of the air flow to reach the purpose of ash removal. The microcomputer automatic control device is used to adjust the ash cleaning cycle and pulse spraying time randomly according to the dust concentration, so that the dust collector can operate within the resistance range. When changing the bag of the wet electrostatic precipitator, open the top bag changing cover and directly pull out the filter bag, which is simple and convenient to protect. Ningbo large Dust removal equipment Wet electrostatic precipitators are mostly used in bag type precipitators. Dust removal bags are installed in the gas box. Wet electrostatic precipitators are mostly external filter type. Dust is collected in the ash hopper of wet electrostatic precipitators through the injection of pulse solenoid valves. The wet electrostatic precipitator is installed in a simple structure. This device is planned as an internal filtering structure, which can change the external pressure of the wet electrostatic precipitator to the internal pressure. In this way, the shell of the wet electrostatic precipitator can be structured without external iron plate sealing, which saves costs and does not hinder the use of the wet electrostatic precipitator. The processing of wet electrostatic precipitator is particularly important. In recent years, some Dust removal equipment manufactor Small manufacturers use small sewing machines as processing equipment, and use low-quality thread as raw materials during processing, which is fake, and the processing level is far behind. The wet electrostatic precipitator will open lines, cracks, and drop the bottom after a short time of operation. Although the size of the cloth bag is slightly smaller, it can also be used, but after absorbing the dust with large specific gravity, the bag will drop after a period of use.
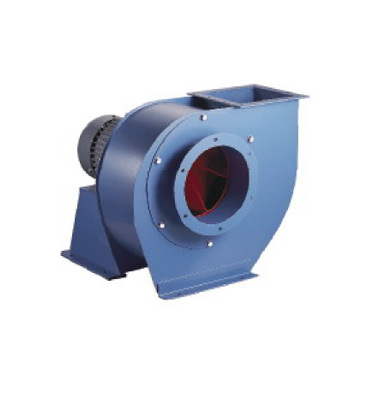
The fan is allowed to start at full voltage or at reduced voltage, but it should be noted that the current at full voltage starting is about 5~7 times the rated current, and the reduced voltage starting torque is proportional to the square of the current. When the grid capacity is insufficient, the reduced voltage starting should be used. (When the power is greater than 11KW, it is advisable to adopt the step-down starting.) When the fan is in test run, Dust removal equipment manufactor Carefully read the product manual and check whether the wiring method is consistent with the wiring diagram; Carefully check whether the working voltage of the power supply to the fan meets the requirements, whether the power supply is out of phase or in phase, and whether the capacity of the electrical components provided meets the requirements. During commissioning, the number of people shall not be less than two. One person shall control the power supply and the other person shall observe the operation of the fan. If any abnormality is found, stop the machine immediately for inspection; First, check whether the rotation direction is correct; After the fan starts to run, immediately check whether the running current is balanced and whether the current exceeds the rated current; large Dust removal equipment If there is no normal phenomenon, stop the machine for inspection. After five minutes of operation, stop the machine to check whether the fan is abnormal, and start the machine again after confirming that there is no abnormal phenomenon. When the two speed fan is tested, start the low speed fan first and check whether the rotation direction is correct; When starting the high-speed train, the fan must be stopped before starting to prevent the switch tripping and motor damage caused by high-speed reverse rotation. When the fan reaches the normal speed, check whether the input current of the fan is normal, and the operating current of the fan cannot exceed its rated current. If the operating current exceeds its rated current, check whether the voltage supplied to the fan is normal. The motor power required by the fan refers to the higher power required for centrifugal fan and fan box when the air inlet is fully open under certain working conditions. If the air inlet is fully opened for operation, the motor may be damaged. During fan commissioning, it is better to close the valve on the inlet or outlet pipeline of the fan, open the valve gradually after operation until the required working condition is reached, and pay attention to whether the operating current of the fan exceeds the rated current
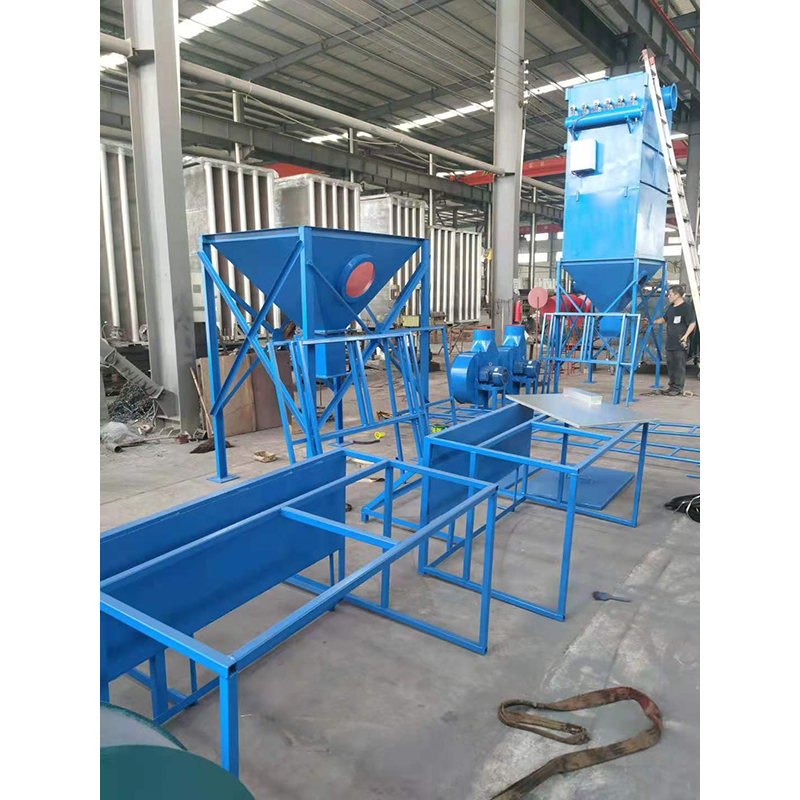
2. The influence of the total pressure deviation Δ H of the fan itself was not considered during selection. When the actual total pressure of the fan was positive deviation, the flow increased; When the actual total pressure of the fan is negative deviation, the flow decreases. See (a) below. The relationship between the deviation of the pipe network characteristic curve and the total pressure and the flow can be eliminated by one of the following methods when the fan starts to officially operate after new installation, or when the flow is too large or too small during use. 1. Use the opening and closing of throttling device to adjust the flow. 2. Increase or decrease the flow by increasing or decreasing the fan speed. 3. Use a new fan with higher or lower pressure to increase or decrease the flow. 4. Change the pipe network to reduce the resistance coefficient of the pipe network to increase the flow. It must be pointed out that throttling devices are generally used to regulate the flow. However, when the actual flow is much larger than the required flow, this method wastes too much power and is very uneconomical. If conditions permit, the fan speed is usually reduced or the fan with lower pressure is replaced. When the throttling device is fully open, the flow is still too small. At this time, the throttling device has lost its function, so try to reduce the resistance coefficient of the pipe network to increase the flow, or increase the fan speed and replace the fan with higher pressure. However, the speed of the fans directly connected to the motor and the coupling cannot be changed generally. Only the fan driven by the pulley can increase or decrease the speed by changing the diameter of the pulley, but the speed of the fan cannot exceed the speed max in the performance and selection table.
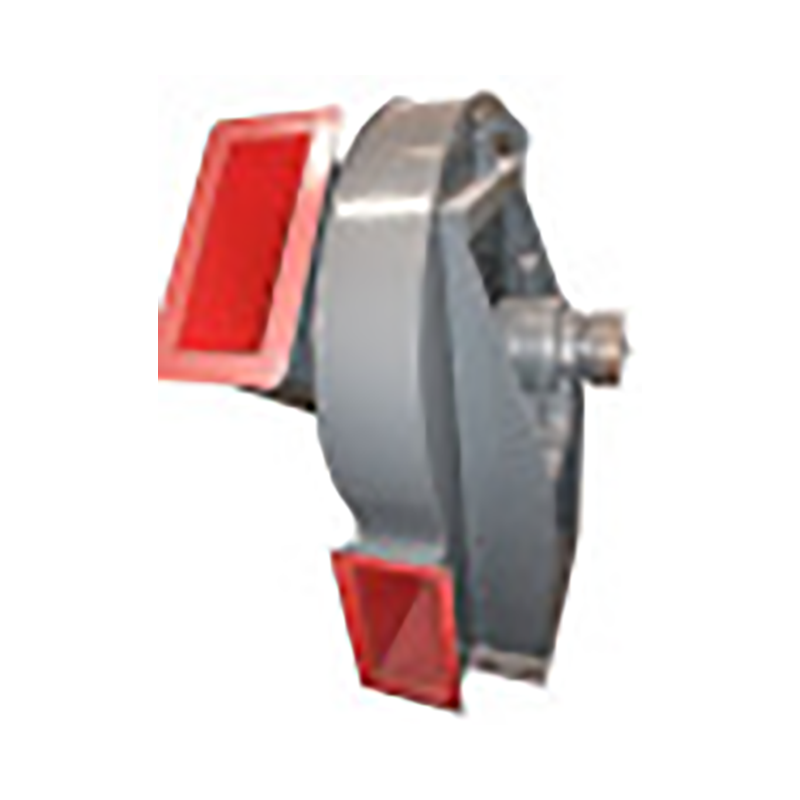
In order to avoid man-made faults and accidents caused by improper maintenance, prevent the occurrence of natural faults and accidents of fans and motors in all aspects, so as to give full play to the efficiency of equipment and extend the service life of equipment, therefore, the maintenance of fans must be strengthened. (1) Working system of fan maintenance The fan maintenance personnel must pay attention to the following points: 1. The fan can only be operated when the fan equipment is completely normal. 2. If the fan equipment starts after maintenance, pay attention to whether all parts of the fan are normal. 3. Regularly clean the dust, dirt, water and other impurities inside the fan and gas transmission pipeline, and check whether the impeller is worn and rusted, if any, repair and replace it in time. 4. Regularly replace the lubricating oil (recommended 3-6 months). It is recommended to add N46 (ISO VG46, 30) in summer and N32 (ISO VG32, 20) in winter. The oil level should be at 1/2 of the oil window. 5. Regularly check (3-6 months is recommended) couplings, pulleys, etc. If parts are found to be worn or rusted, they should be repaired and replaced immediately. 6. The equipment shall not be repaired during operation.