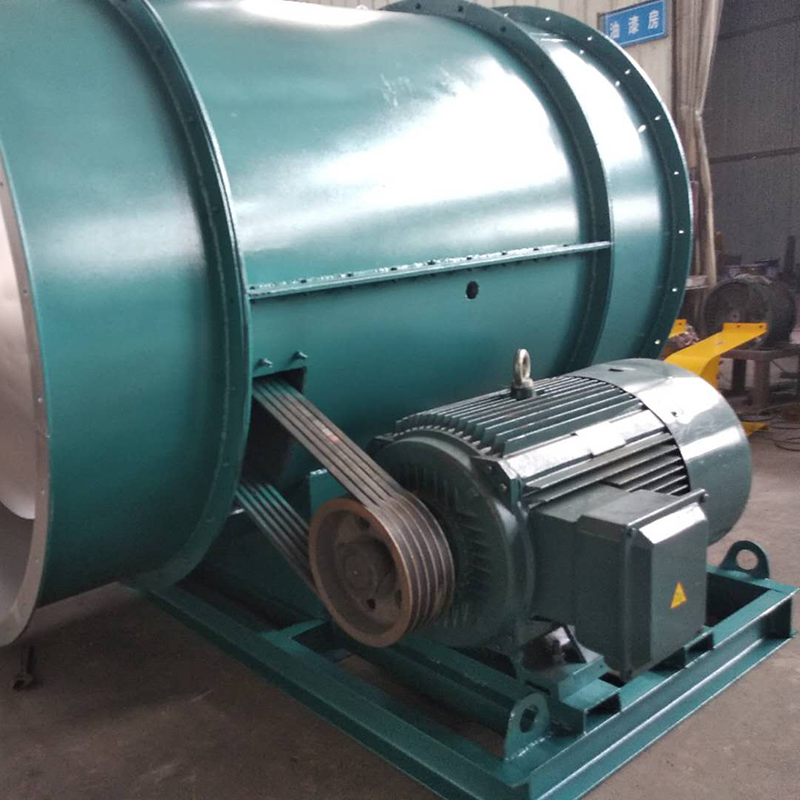
Forecast the demand structure from the main fields. large Centrifugal fan General ventilation fans (generally small and medium-sized centrifugal and axial fans) are the most widely used, with the largest demand and the largest number of manufacturers. In general, the supply of such products exceeds the demand. Although the demand for special purpose fans (including anti-corrosion fans, high-temperature fans, wear-resistant fans, fire smoke exhaust fans, etc.) is not large, due to the special operating environment, they need to be treated differently, because the main material requirements are special. The biggest feature of Roots blower is that when the pressure is adjusted within the allowable range, the flow changes little, the pressure selection range is wide, and it has the characteristics of forced gas transmission. The main disadvantage is that the noise is large. Centrifugal fan company Through technology introduction, joint venture and self-development, China has launched a three blade roots blower with low noise, which is very popular with users and has a good market prospect. Turbine compressor (including centrifugal compressor, axial compressor and axial centrifugal compound compressor) is an important equipment of major engineering complete equipment, which plays an important role in the national economy. The performance of turbine compressor requires high pressure and large flow. With the large-scale of the complete set of equipment, the turbine compressor parameters are required to be higher and higher. Such as blast furnace smelting plant, large coal chemical plant, large fertilizer plant, large ethylene plant, large air separation plant, natural gas pipeline transportation plant and oil field gas injection plant. The demand for such products accounts for a small proportion of the total fan volume, but because of their importance, complex structure, long manufacturing cycle and high technical content, they have relatively good economic and social benefits. Turbine compressor manufacturing level represents the overall level of the fan industry
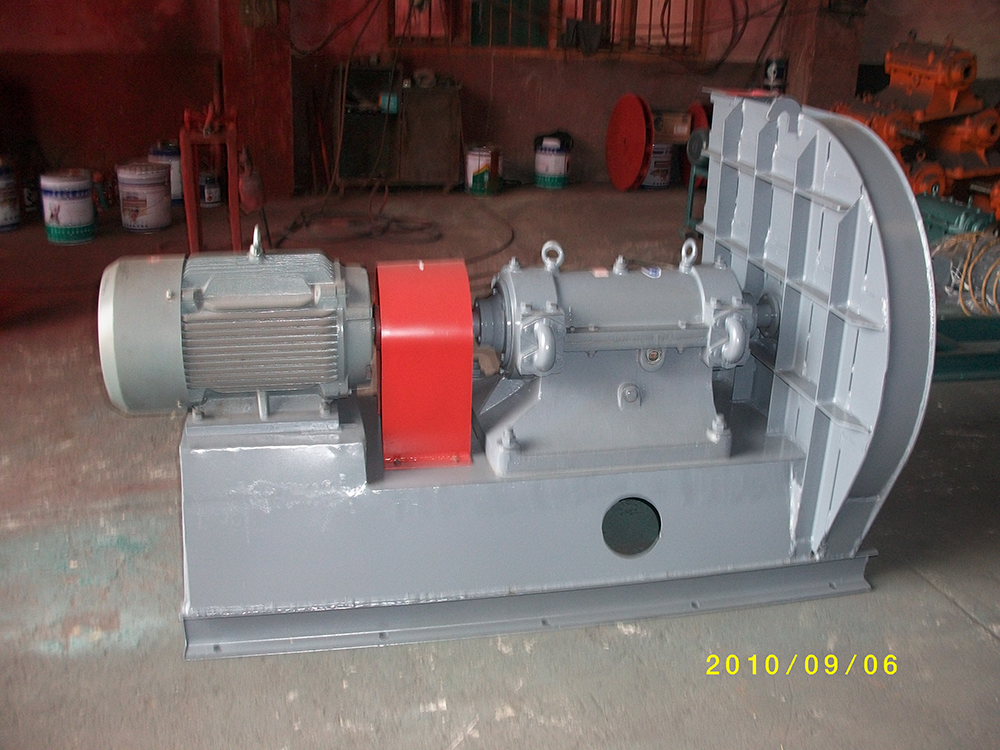
Preparations for fan installation. large Centrifugal fan Before unpacking the fan, check whether the package is intact, whether the nameplate parameters of the fan meet the requirements, and whether all accompanying accessories are complete. Carefully check whether the fan is deformed or damaged during transportation, whether the fasteners are loose or fall off, and whether the impeller is scratched, and check all parts of the fan. Bijie Centrifugal fan company If any abnormality is found, it shall be repaired before use. Use a 500V megger to measure the insulation resistance between the fan housing and the motor winding. The value should be greater than 0.5 megohm. Otherwise, the motor winding should be dried. The temperature during drying should not exceed 120 ℃. Prepare various materials, tools and sites required for fan installation.
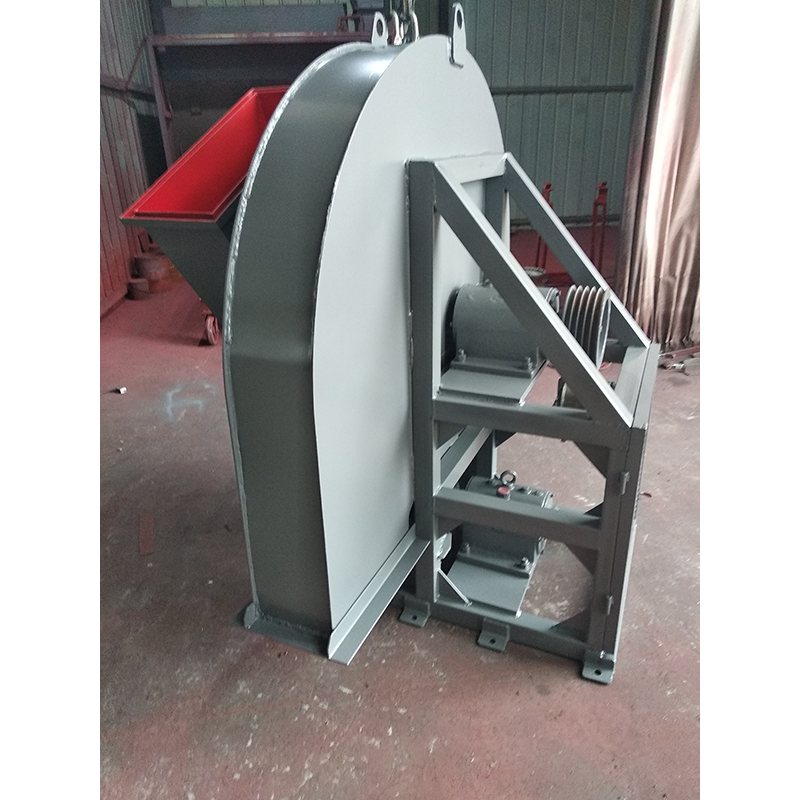
When the bearing temperature of the fan is normal, it is ≤ 70 ℃. If it rises to 70 ℃, an alarm should (will) be given if there is an electric control. At this time, the reason should be found out. First, check whether the cooling water is normal? Is the bearing oil level normal? If the cause cannot be found for a while, the bearing temperature rises rapidly to 90 ℃, and if there is an electric control, the alarm and shutdown signal shall be sent again. Bijie Centrifugal fan In the process of fan startup, shutdown or operation, if any abnormal phenomenon is found, it shall be checked immediately. If any small fault is found during the check, it shall be timely found out the cause and eliminated. In case of major fault (such as severe vibration, impact of fan, sharp rise of bearing temperature, etc.), stop the machine immediately for inspection. large Centrifugal fan The lubricating oil (or grease) shall be renewed and replaced one month after the first operation of the fan. In addition to replacement after each overhaul, the lubricating oil (or grease) can be replaced once every 1~2 months under normal conditions, or according to the actual situation. Fans include fans, turbine blowers, roots blowers and turbine compressors, which are divided into 7 categories in detail, including centrifugal compressors, axial compressors, centrifugal blowers, roots blowers, centrifugal fans, axial fans and Ye's blowers
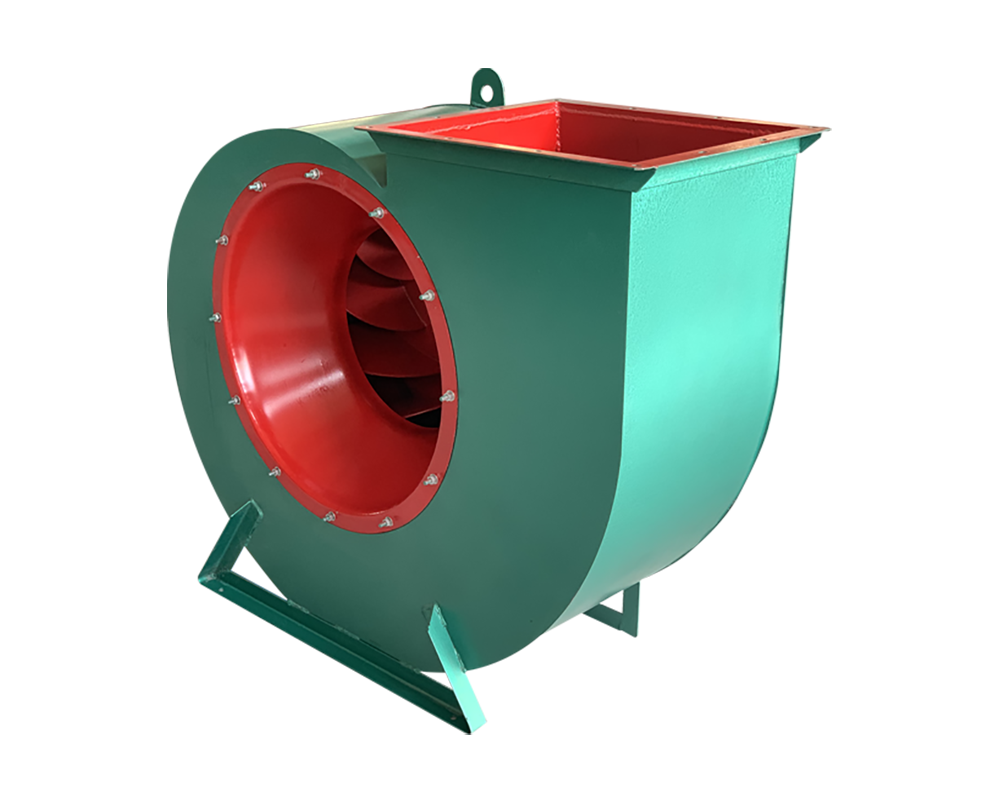
Correct maintenance is an important guarantee for the safe and reliable operation of the fan and the improvement of its service life. Therefore, Centrifugal fan company When using fans, full attention must be paid. Impeller maintenance: at the initial stage of impeller operation and during all regular inspections, whenever there is an opportunity, the impeller must be checked for cracks, wear, dust and other defects. The impeller must be kept clean whenever possible, large Centrifugal fan The steel wire brush shall be used regularly to remove the dust and rust on the impeller. As the travel time increases, the dust can not be evenly attached to the impeller, which will cause damage to the balance of the impeller and even cause rotor vibration. As long as the impeller is repaired, it needs to be dynamically balanced again. If possible, the portable trial dynamic balancing instrument can be used for on-site balancing. Before dynamic balancing, check whether all fastening bolts are tightened. Since the impeller has been operating in an unbalanced state for a period of time, these bolts may have become loose. Bearing maintenance: frequently check the oil supply of bearing lubricating oil. If the box leaks oil, tighten the bolts of the end cover a little. If this is not enough, you may have to use new sealing packing. When the bearing lubricating oil is in normal use, it should be replaced at least once every six months. When it is used for the first time, it should be done after 200 hours of operation. The second oil change should be done in 1 to 2 months. After that, the lubricating oil should be checked once a week. If the lubricating oil does not deteriorate, the oil change can be extended to 2 to 4 months. The specified brand of lubricating oil (specified on the general drawing) must be used when replacing, The old oil in the oil tank shall be completely drained and cleaned before new oil can be filled. If the fan bearing needs to be replaced, pay attention to the following matters: before installing the new bearing, the bearing and bearing box must be very clean. Place the bearing in the oil with a temperature of about 70~80 ℃ and heat it before installing it on the shaft. Do not force assembly to avoid damaging the shaft. Maintenance of other supporting equipment: see the respective user manual for the maintenance of various supporting equipment, including motors, electric actuators, instruments, meters, etc. These operating instructions are provided by each supporting manufacturer. The manufacturer will pack these instructions together and provide them to the user
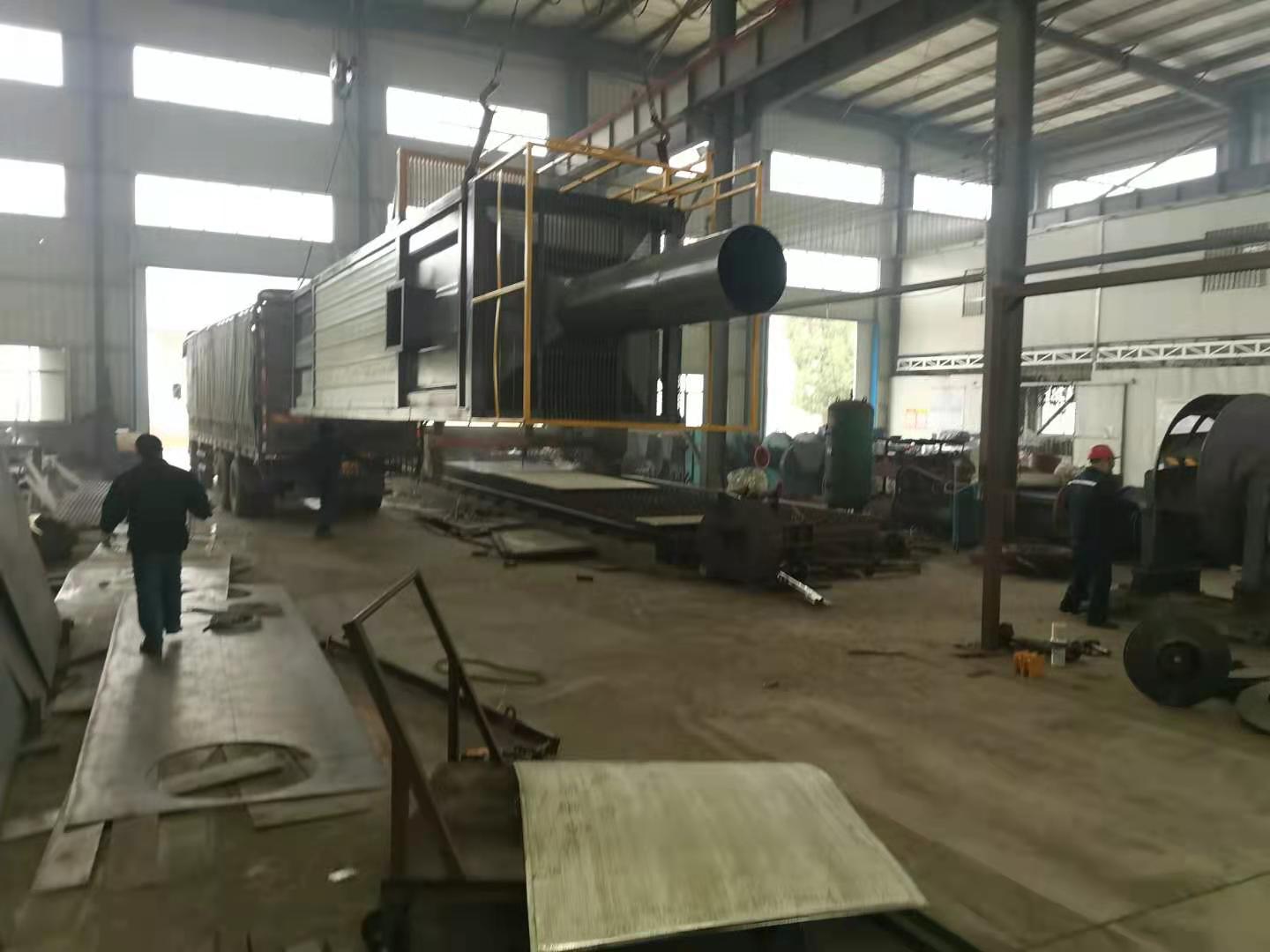
Main factors affecting the dust removal efficiency of wet electrostatic precipitator. The effect of electrostatic voltage, water volume and dust concentration on wet electrostatic precipitation efficiency is positive, that is, the dust removal efficiency increases with the increase of voltage, water volume and dust concentration. Among them, voltage has the most significant effect on dust removal efficiency, followed by water volume, and dust concentration has the least effect. The combination of static electricity and water mist can significantly improve the dust removal efficiency. The role of water in wet electrostatic precipitation. The water in wet electrostatic precipitator mainly exists as atomized water droplets. According to domestic research, water mist has a series of effects on the improvement of dust removal efficiency of wet electrostatic precipitator, large Centrifugal fan Main mechanism: the water mist can keep the discharge electrode clean and keep the corona vigorous; The mist particles strike the dust collecting electrode to form a thin and uniform water film, Bijie Centrifugal fan It can prevent the "secondary flying" of low specific resistance dust from tempering high specific resistance dust and prevent the occurrence of "reverse corona"; For the dust with strong viscosity, the electrode can be prevented from sticking; It is also suitable for collecting those flammable and explosive dust. The water mist is sprayed directly to the discharge electrode and corona area, and the discharge electrode also acts as an atomizer. The same power supply can realize corona discharge, water atomization, water mist and dust particle charging, realizing the organic combination of static electricity and water mist. The water mist is directly sprayed to the discharge electrode, which has a high charge. The collision interception, adsorption and coagulation of water mist with high charge mass ratio in the electric field can greatly improve the dust removal efficiency. The water mist strikes the dust collecting electrode to form water flow down, so that the dust collecting electrode is always kept clean, eliminating the vibrating device, and avoiding a series of problems caused by vibrating dust removal in dry dust removal. In the method of spraying water mist to the discharge electrode and corona area to further atomize the water mist, the static electricity does not directly contact the spray device, so there is almost no insulation problem. This method is completely different from the dedusting technology of "corona discharge atomizes water". The latter is almost impossible to insulate due to the direct contact between water and electricity, and it is actually difficult to achieve industrial application. The barbed electrode can produce a strong electrostatic field, and has a good corona discharge capacity. The electrostatic and water mist work together, and has a high dust removal efficiency