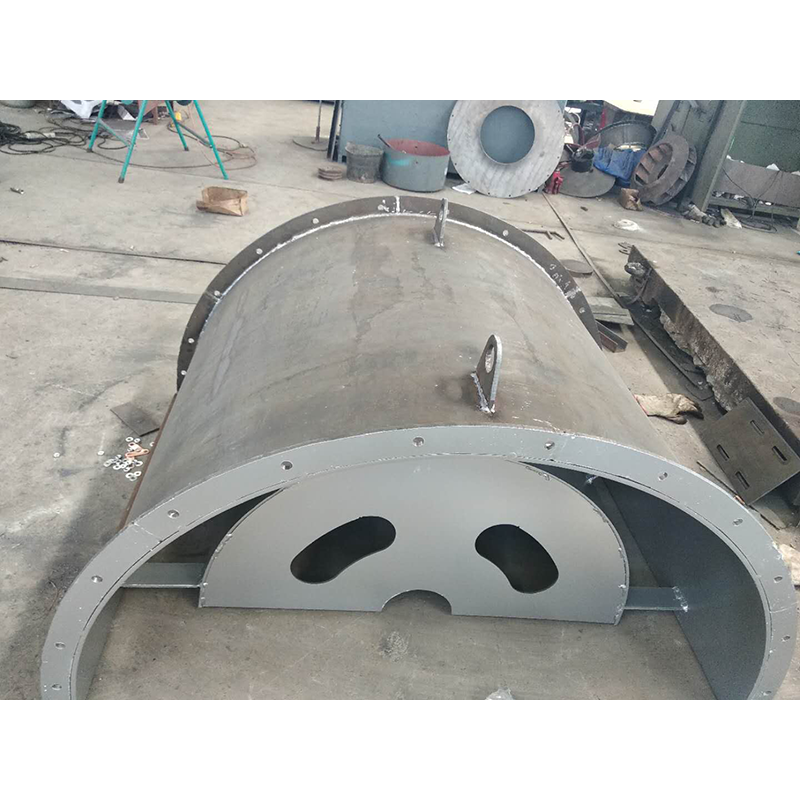
3. When installing Type C and Type B, ensure that the two pulley positions are on the same plane, and the flatness tolerance is 0.5mm. 4. When installing Type D, use a dial indicator and feeler gauge to measure the coaxiality of the fan spindle and motor spindle and the parallelism of both ends of the coupling. The coaxiality tolerance of two shafts is 0.2mm, the parallelism tolerance of both ends of the coupling is 0.2mm, and the spacing between two planes of the coupling is 5 to 8mm. 5. After the fan is installed, move the rotor with hand or lever to check whether it is too tight or collided. The test run can be carried out without overtightening or collision. 6. After the motor is installed, the belt pulley or coupling guard shall be installed. If the air inlet is not connected to the air inlet pipe, the guard net or other safety devices (provided by the user) shall also be provided. 7. Other parts shall be installed according to the corresponding positions in the drawing. 8. Add N46 (ISO VG46, 30) in summer and N32 (ISO VG32, 20) in winter. The oil level should be at 1/2 of the oil window.
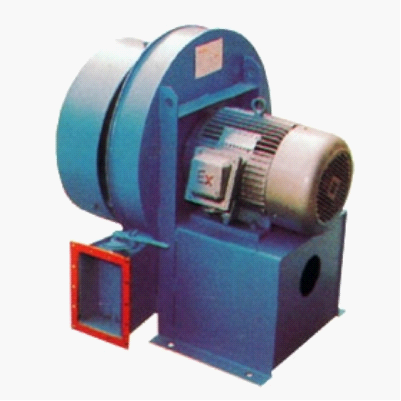
Industrial dust collector manufactor Forecast from the characteristics of fan demand. large Industrial dust collector For small and medium-sized fans with large usage and wide range, the product structure and manufacturing process are relatively simple, and the cost is also low. Users mainly pursue high efficiency, low noise, long life, and low price. The other is capital and technology intensive. The product structure is complex, the manufacturing cycle is long, and the completeness and systematicness are also strong. Moreover, it operates under high pressure, high temperature and high speed conditions, and some even operate under severe conditions. Users have different requirements for this type of fan. For turbine blowers, compressors and large ventilators, users mainly pursue high quality, high reliability, smooth operation and long cycle
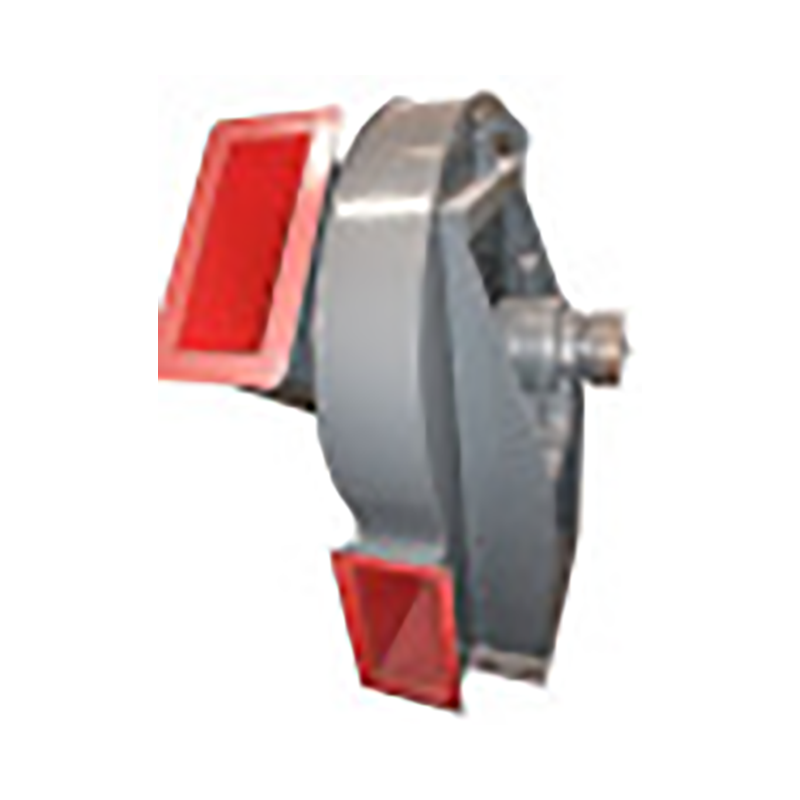
The wet electrostatic precipitator is a new kind of dust removal equipment used to treat micro dust and micro particles, large Industrial dust collector It is mainly used to remove dust, acid mist, water droplets, aerosols, odor, PM2.5 and other harmful substances in humid gases, and is an ideal equipment for controlling atmospheric dust pollution. The wet electrostatic precipitator is usually referred to as WESP, which has the same basic principle as the dry electrostatic precipitator. It goes through three stages: charging, collection and dust removal. The principle of wet electrostatic precipitator is the same as that of dry electrostatic precipitator, Tongling Industrial dust collector The dust is charged by high-voltage corona discharge, and the charged dust reaches the dust collecting plate/tube under the action of electric field force. The dry electrostatic precipitator mainly deals with dry gas with very low water content, while the wet electrostatic precipitator mainly deals with wet gas with high water content or even saturation. There is a big difference between WESP and DESP in the way of removing the dust collected on the dust collecting plate/pipe. The dry electrostatic precipitator generally uses mechanical rapping or acoustic cleaning to remove the dust on the electrode, while the wet electrostatic precipitator uses regular flushing to remove the dust along with the flow of flushing fluid
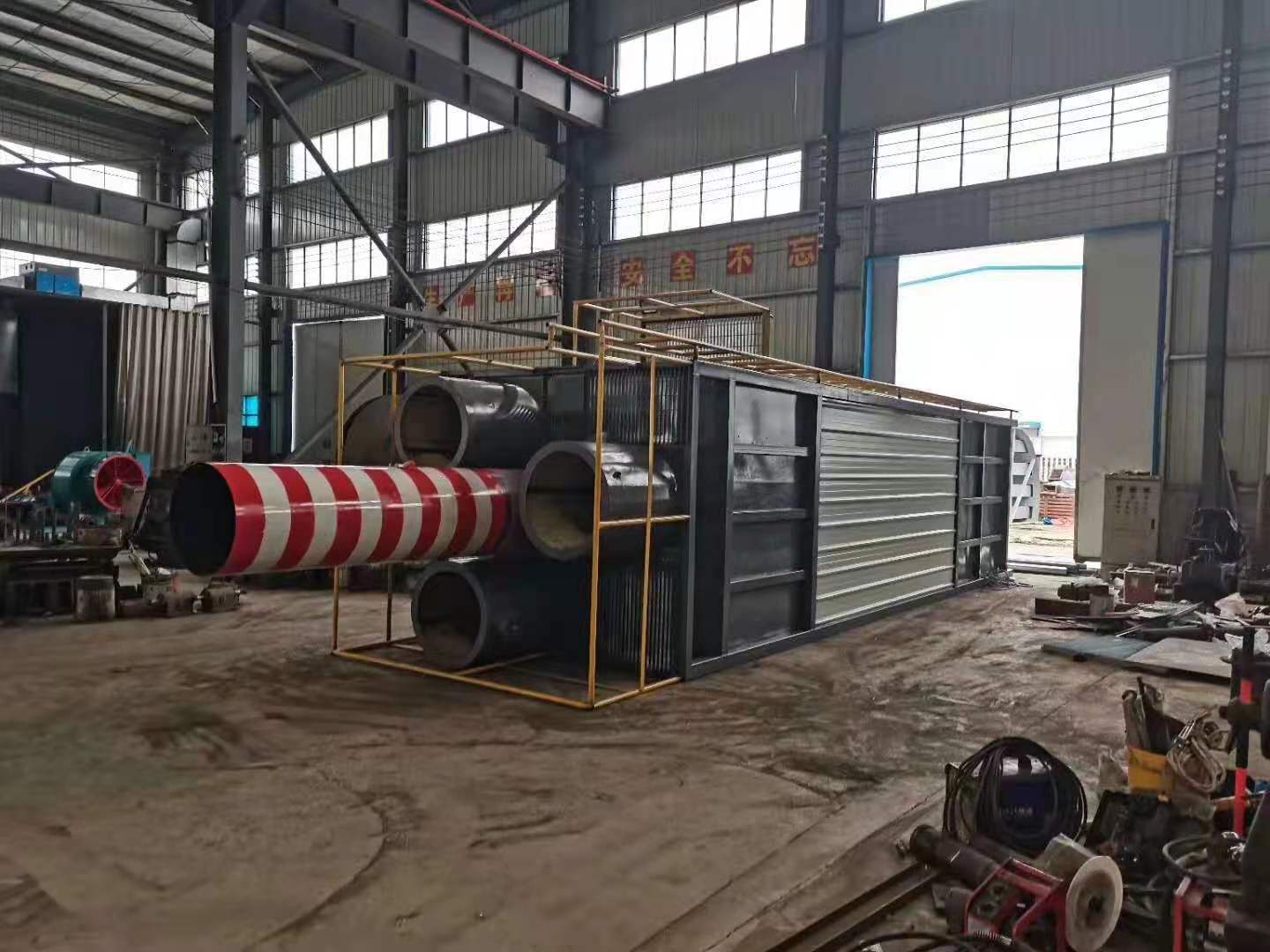
Correct maintenance is an important guarantee for the safe and reliable operation of the fan and the improvement of its service life. Therefore, Industrial dust collector manufactor When using fans, full attention must be paid. Impeller maintenance: at the initial stage of impeller operation and during all regular inspections, whenever there is an opportunity, the impeller must be checked for cracks, wear, dust and other defects. The impeller must be kept clean whenever possible, large Industrial dust collector The steel wire brush shall be used regularly to remove the dust and rust on the impeller. As the travel time increases, the dust can not be evenly attached to the impeller, which will cause damage to the balance of the impeller and even cause rotor vibration. As long as the impeller is repaired, it needs to be dynamically balanced again. If possible, the portable trial dynamic balancing instrument can be used for on-site balancing. Before dynamic balancing, check whether all fastening bolts are tightened. Since the impeller has been operating in an unbalanced state for a period of time, these bolts may have become loose. Bearing maintenance: frequently check the oil supply of bearing lubricating oil. If the box leaks oil, tighten the bolts of the end cover a little. If this is not enough, you may have to use new sealing packing. When the bearing lubricating oil is in normal use, it should be replaced at least once every six months. When it is used for the first time, it should be done after 200 hours of operation. The second oil change should be done in 1 to 2 months. After that, the lubricating oil should be checked once a week. If the lubricating oil does not deteriorate, the oil change can be extended to 2 to 4 months. The specified brand of lubricating oil (specified on the general drawing) must be used when replacing, The old oil in the oil tank shall be completely drained and cleaned before new oil can be filled. If the fan bearing needs to be replaced, pay attention to the following matters: before installing the new bearing, the bearing and bearing box must be very clean. Place the bearing in the oil with a temperature of about 70~80 ℃ and heat it before installing it on the shaft. Do not force assembly to avoid damaging the shaft. Maintenance of other supporting equipment: see the respective user manual for the maintenance of various supporting equipment, including motors, electric actuators, instruments, meters, etc. These operating instructions are provided by each supporting manufacturer. The manufacturer will pack these instructions together and provide them to the user