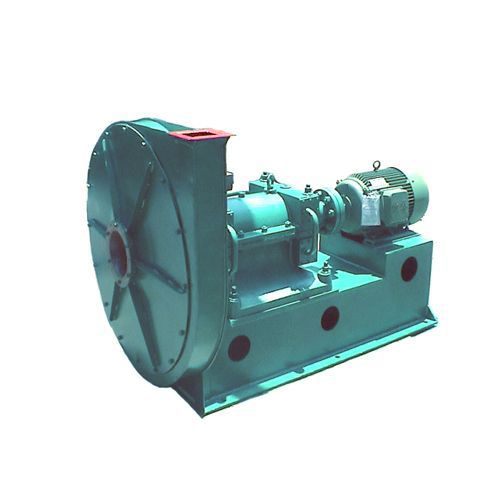
The wet electrostatic precipitator is a new kind of dust removal equipment used to treat micro dust and micro particles, major Axial flow fan It is mainly used to remove dust, acid mist, water droplets, aerosols, odor, PM2.5 and other harmful substances in humid gases, and is an ideal equipment for controlling atmospheric dust pollution. The wet electrostatic precipitator is usually referred to as WESP, which has the same basic principle as the dry electrostatic precipitator. It goes through three stages: charging, collection and dust removal. The principle of wet electrostatic precipitator is the same as that of dry electrostatic precipitator, Xiangtan Axial flow fan The dust is charged by high-voltage corona discharge, and the charged dust reaches the dust collecting plate/tube under the action of electric field force. The dry electrostatic precipitator mainly deals with dry gas with very low water content, while the wet electrostatic precipitator mainly deals with wet gas with high water content or even saturation. There is a big difference between WESP and DESP in the way of removing the dust collected on the dust collecting plate/pipe. The dry electrostatic precipitator generally uses mechanical rapping or acoustic cleaning to remove the dust on the electrode, while the wet electrostatic precipitator uses regular flushing to remove the dust along with the flow of flushing fluid
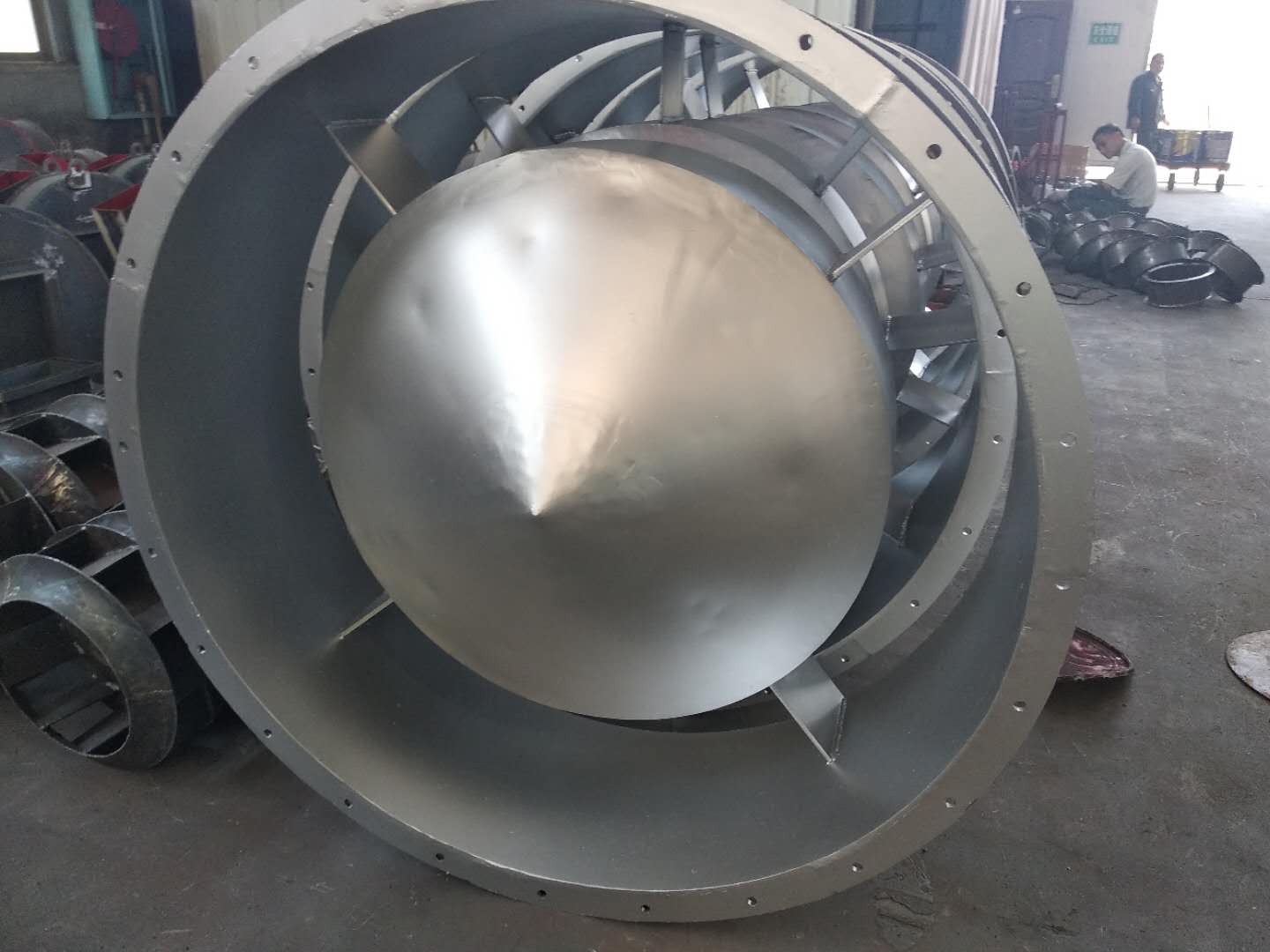
How are dust collectors classified, major Axial flow fan Do you know how to distinguish it and how to define its economic type? Let's talk about it from these aspects. 1. Dust removal efficiency. Xiangtan Axial flow fan Dust removal efficiency refers to the ratio of the amount of dust collected by the dust collector to the amount of dust entering the dust collector. According to the total dedusting efficiency, the dedusters can be divided into: low efficiency dedusters (50~80%), medium efficiency dedusters (80~95%) and high efficiency dedusters (more than 95%). 2. Dust removal resistance. The resistance indicates the pressure loss when the airflow passes through the dust remover. According to the resistance, dust collectors can be divided into low resistance dust collectors (Δ P<500Pa), medium resistance dust collectors (Δ P=500 ~ 2000Pa) and high resistance dust collectors (Δ P=2000 ~ 20000Pa). 3. Economy. Economy is one of the important indexes for evaluating dust remover, which includes equipment cost and operation and maintenance cost of dust remover. Among all kinds of dust collectors, the equipment cost of electrostatic precipitator is the highest, followed by bag type dust collector, Venturi tube dust collector, cyclone dust collector is the lowest electrostatic precipitator: the dust removal efficiency is high, generally above 99%, and the design efficiency is up to 99.99%. The wet dust collector is commonly known as "water dust collector" : The filtration efficiency can reach more than 85%, and the integrated desulfurization and dust remover of stone water film+swirl plate>>about 80% of desulfurization and dust removal can reach as high as about 95%.
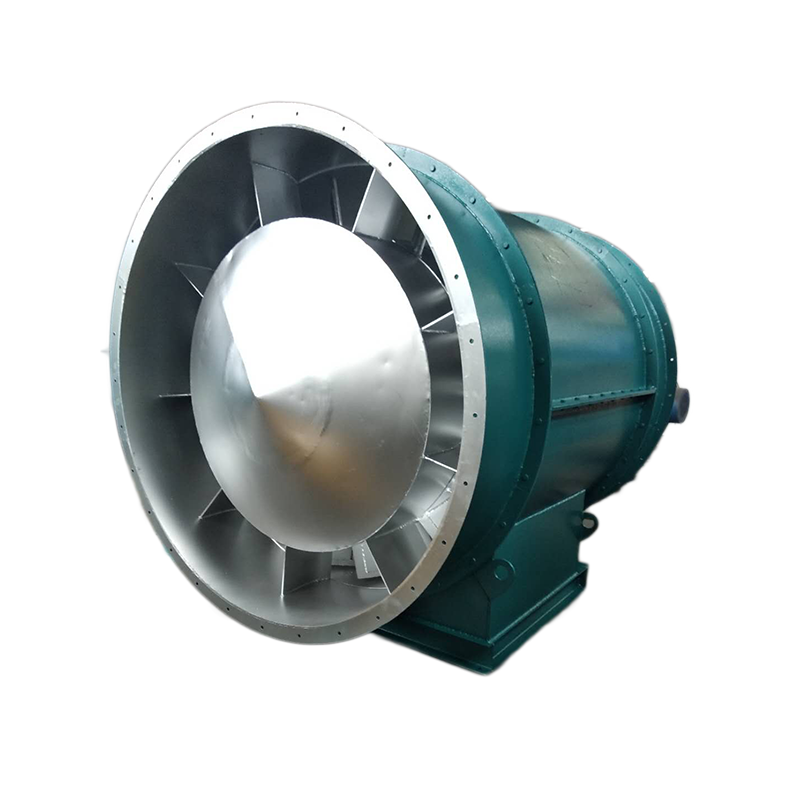
2. The influence of the total pressure deviation Δ H of the fan itself was not considered during selection. When the actual total pressure of the fan was positive deviation, the flow increased; When the actual total pressure of the fan is negative deviation, the flow decreases. See (a) below. The relationship between the deviation of the pipe network characteristic curve and the total pressure and the flow can be eliminated by one of the following methods when the fan starts to officially operate after new installation, or when the flow is too large or too small during use. 1. Use the opening and closing of throttling device to adjust the flow. 2. Increase or decrease the flow by increasing or decreasing the fan speed. 3. Use a new fan with higher or lower pressure to increase or decrease the flow. 4. Change the pipe network to reduce the resistance coefficient of the pipe network to increase the flow. It must be pointed out that throttling devices are generally used to regulate the flow. However, when the actual flow is much larger than the required flow, this method wastes too much power and is very uneconomical. If conditions permit, the fan speed is usually reduced or the fan with lower pressure is replaced. When the throttling device is fully open, the flow is still too small. At this time, the throttling device has lost its function, so try to reduce the resistance coefficient of the pipe network to increase the flow, or increase the fan speed and replace the fan with higher pressure. However, the speed of the fans directly connected to the motor and the coupling cannot be changed generally. Only the fan driven by the pulley can increase or decrease the speed by changing the diameter of the pulley, but the speed of the fan cannot exceed the speed max in the performance and selection table.
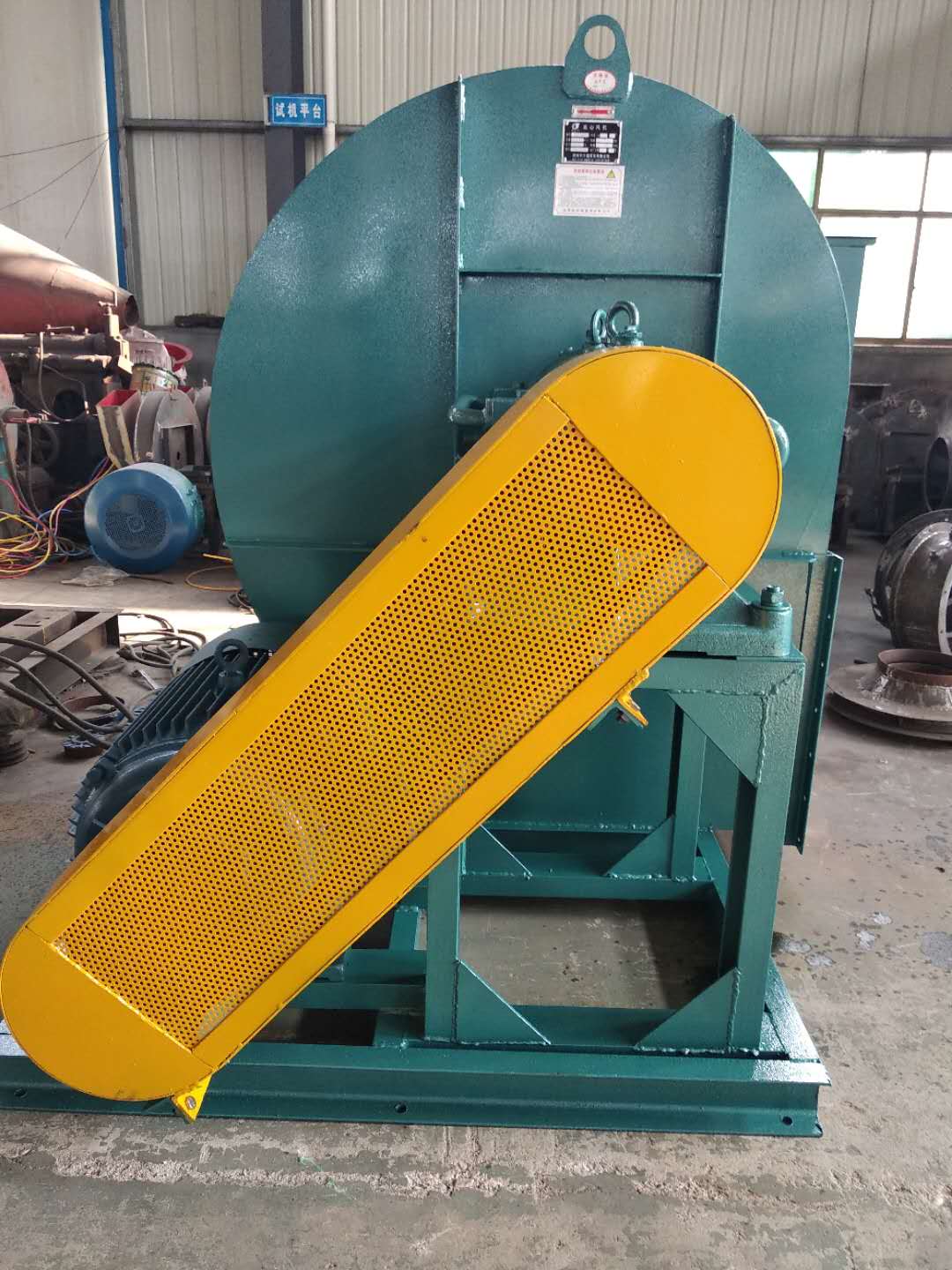
In order to avoid man-made faults and accidents caused by improper maintenance, prevent the occurrence of natural faults and accidents of fans and motors in all aspects, so as to give full play to the efficiency of equipment and extend the service life of equipment, therefore, the maintenance of fans must be strengthened. (1) Working system of fan maintenance The fan maintenance personnel must pay attention to the following points: 1. The fan can only be operated when the fan equipment is completely normal. 2. If the fan equipment starts after maintenance, pay attention to whether all parts of the fan are normal. 3. Regularly clean the dust, dirt, water and other impurities inside the fan and gas transmission pipeline, and check whether the impeller is worn and rusted, if any, repair and replace it in time. 4. Regularly replace the lubricating oil (recommended 3-6 months). It is recommended to add N46 (ISO VG46, 30) in summer and N32 (ISO VG32, 20) in winter. The oil level should be at 1/2 of the oil window. 5. Regularly check (3-6 months is recommended) couplings, pulleys, etc. If parts are found to be worn or rusted, they should be repaired and replaced immediately. 6. The equipment shall not be repaired during operation.