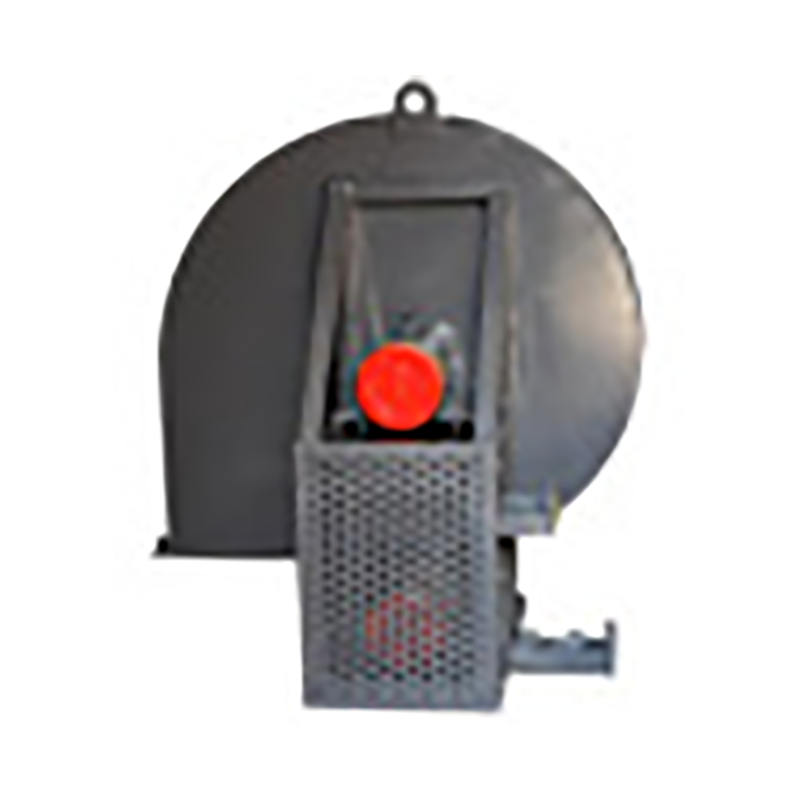
While meeting the new standard, the wet electrostatic precipitator can also control the haze fine particles, sulfur trioxide aerosol droplets, organic pollutants, heavy metal pollutants, etc., which has great social benefits. The air pollutant control mode of SCR+ESP/FF+WFGD+WESP is also a relatively effective way to control pollutants in Shangshan Coal fired Power Plant. Centrifugal fan manufactor Common dust control technologies, among which the dry electrostatic precipitator, the electrostatic fabric composite precipitator and the bag type precipitator are used as the front section dust control technology, cannot guarantee the ultra clean emission of flue gas dust after the desulfurization device, while the wet electrostatic precipitator arranged at the downstream of the wet desulfurization device will be used as a reliable terminal dust control technology. The working principle of wet electrostatic precipitator is similar to that of dry electrostatic precipitator. It is high-voltage corona discharge that charges dust or water mist, and charged particles reach the dust collecting plate under the action of electric field force, major Centrifugal fan However, in terms of the way of dust, the dry electrostatic precipitator uses mechanical vibration, while the wet electrostatic precipitator uses flushing fluid to flush electricity, washing the dust captured on the dust collection plate into the ash hopper and then discharging the wet electrostatic precipitator. The advantages of the wet electrostatic precipitator are: because the mass and heat transfer processes occur simultaneously in the process of gas and liquid contact, this type of precipitator has the function of dust removal, It also has the function of flue gas cooling and absorption of harmful gases. Suitable for high temperature. High temperature, flammable, explosive and harmful gases; Normal operation and high purification efficiency; Dust and gas that can be used for gathering fog and dust; Exhaust volume balance; Simple structure. Low investment, convenient operation and maintenance.

According to the report data released by the Global Wind Energy Council, the new installed capacity of global wind power in 2014 was 51477MW, up 44% year on year, and the cumulative installed capacity exceeded the threshold of 50GW for the first time. All data set new world records. China's wind power industry has driven global growth. In 2014, China's new installed capacity of wind power was 23350500 kilowatts, 45.1% higher than that of the previous year, major Centrifugal fan The cumulative installed capacity has reached nearly 115 million kilowatts, of which the grid connected capacity is nearly 100 million kilowatts, accounting for 7% of the total installed power generation capacity. In addition to the strength of wind power itself, the recovery of the wind power industry has also contributed to the decline of coal prices. The decline of fuel costs has led to the profitability of most power enterprises hitting a new high in 2014, Centrifugal fan manufactor This can expand the scale of wind power construction and accelerate the payment of unit arrears. As a result, the performance of wind power equipment manufacturers was in full swing in 2014, the market concentration was further improved to the top eight complete machine enterprises, and China's wind power industry basically ended the situation of low price competition. The wind power industry generally believes that the wind power industry will enter a new normal of stable growth in the future. In the next five years, the annual new installed capacity may reach at least 20 million kilowatts, and there is still a bottleneck for developers to improve their profits.
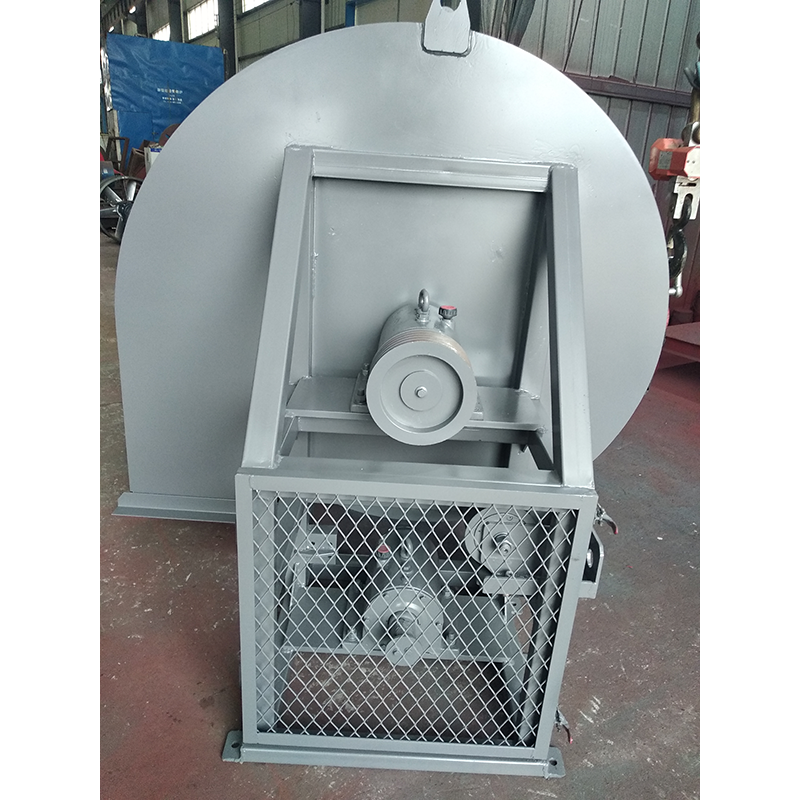
Centrifugal fan manufactor Forecast from the characteristics of fan demand. major Centrifugal fan For small and medium-sized fans with large usage and wide range, the product structure and manufacturing process are relatively simple, and the cost is also low. Users mainly pursue high efficiency, low noise, long life, and low price. The other is capital and technology intensive. The product structure is complex, the manufacturing cycle is long, and the completeness and systematicness are also strong. Moreover, it operates under high pressure, high temperature and high speed conditions, and some even operate under severe conditions. Users have different requirements for this type of fan. For turbine blowers, compressors and large ventilators, users mainly pursue high quality, high reliability, smooth operation and long cycle
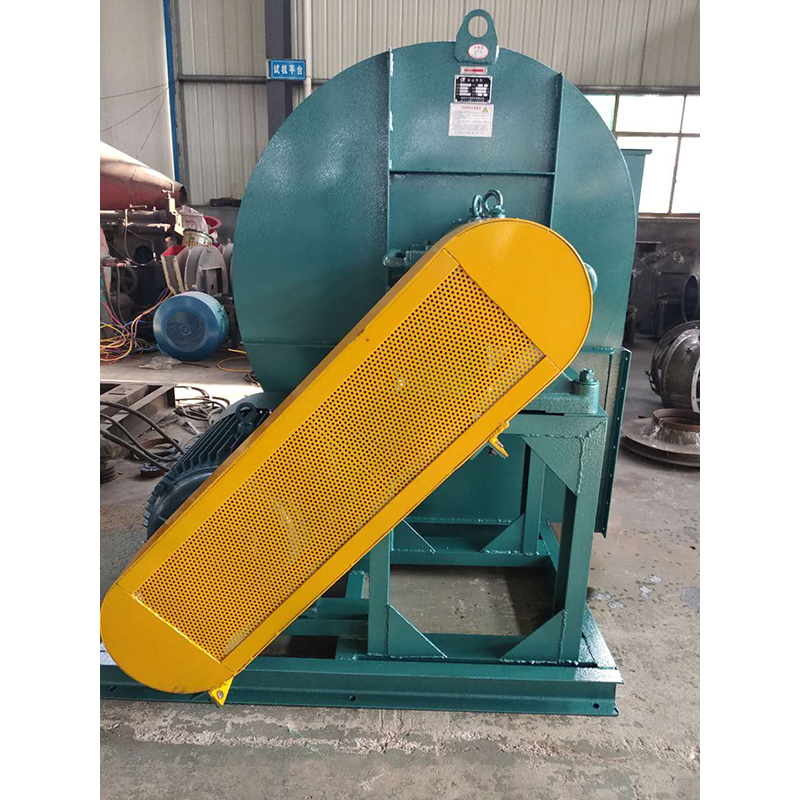
Baise major Centrifugal fan Installation requirements a. The foundation of the fan shall be level and solid, and the foundation height shall be ≥ 200mm. b、 The fan and air duct shall be connected by flexible hose (flexible material and non combustible), the length shall not be less than 200mm, and the pipe diameter shall be the same as the inlet and outlet size of the fan. In order to ensure that the hose will not be twisted or deformed during the system operation, it should be installed with appropriate tightness. The canvas hose installed at the suction end of the fan can be slightly tightened to prevent the fan from being sucked in during operation and reduce the sectional size of the canvas hose. c、 Centrifugal fan manufactor The steel support of the fan must be fixed on the concrete foundation, and a rubber damping pad must be added between the steel support of the fan and the foundation. All fan and motor components are installed on the whole steel support, and the steel ground frame is installed on the damping pad at the top of the foundation. The damping pad is preferably made of perforated rubber plates. d、 The pipe diameter at the outlet of the fan can only be increased, but not decreased. At the end of the outlet, an insect screen should be installed. When the fan is inclined to the upper outlet, a rain cap should be added
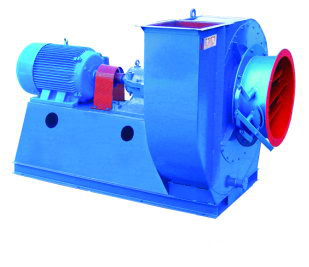
major Centrifugal fan Common fault: the working medium of the fan in the cement industry often contains a certain amount of homogeneous particles with different sizes and shapes, such as the induced draft fan of the dust removal system and the blower for pneumatic conveying. Because these fans work in the dusty air flow, the dust particles in the air flow will not only wear the fan, but also attach ash on the fan blades, and the wear and ash deposition are uneven. As a result, the balance of the fan rotor is destroyed, which causes the fan vibration and shortens the life of the fan. In serious cases, the fan can not work normally. In particular, the fan blades are most severely worn, Centrifugal fan manufactor It not only destroys the flow characteristics in the fan, but also easily leads to major accidents such as blade fracture and runaway. The wear of transmission parts is also a common problem of fans, including various shafts, rollers, reducers, motors, pumps and other bearing positions, bearing seats, keyways, threads and other parts. The traditional repair welding machine processing method is easy to cause material damage, resulting in deformation or fracture of parts, with greater limitations; Brush plating and spray re machining methods often require outsourcing, which not only requires long repair cycle and high cost, but also can not fundamentally solve the causes of wear (poor impact resistance and yield of metal) because the repair materials are metal materials; Many parts can only be scrapped and replaced, which greatly increases the production cost and inventory of spare parts, leaving the enterprise's good resource advantage idle and wasted
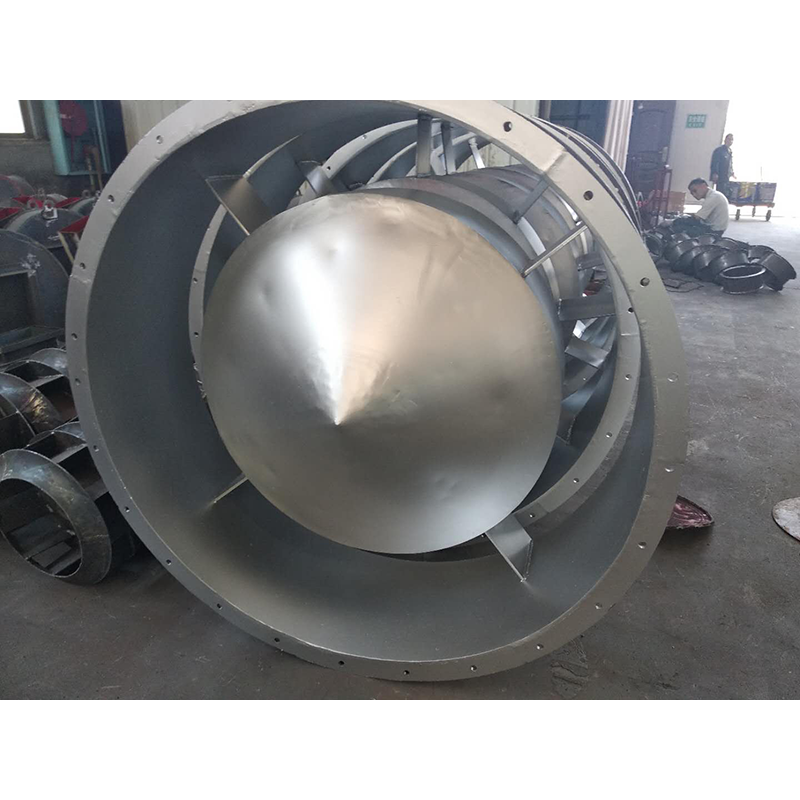
Correct maintenance is an important guarantee for the safe and reliable operation of the fan and the improvement of its service life. Therefore, Centrifugal fan manufactor When using fans, full attention must be paid. Impeller maintenance: at the initial stage of impeller operation and during all regular inspections, whenever there is an opportunity, the impeller must be checked for cracks, wear, dust and other defects. The impeller must be kept clean whenever possible, major Centrifugal fan The steel wire brush shall be used regularly to remove the dust and rust on the impeller. As the travel time increases, the dust can not be evenly attached to the impeller, which will cause damage to the balance of the impeller and even cause rotor vibration. As long as the impeller is repaired, it needs to be dynamically balanced again. If possible, the portable trial dynamic balancing instrument can be used for on-site balancing. Before dynamic balancing, check whether all fastening bolts are tightened. Since the impeller has been operating in an unbalanced state for a period of time, these bolts may have become loose. Bearing maintenance: frequently check the oil supply of bearing lubricating oil. If the box leaks oil, tighten the bolts of the end cover a little. If this is not enough, you may have to use new sealing packing. When the bearing lubricating oil is in normal use, it should be replaced at least once every six months. When it is used for the first time, it should be done after 200 hours of operation. The second oil change should be done in 1 to 2 months. After that, the lubricating oil should be checked once a week. If the lubricating oil does not deteriorate, the oil change can be extended to 2 to 4 months. The specified brand of lubricating oil (specified on the general drawing) must be used when replacing, The old oil in the oil tank shall be completely drained and cleaned before new oil can be filled. If the fan bearing needs to be replaced, pay attention to the following matters: before installing the new bearing, the bearing and bearing box must be very clean. Place the bearing in the oil with a temperature of about 70~80 ℃ and heat it before installing it on the shaft. Do not force assembly to avoid damaging the shaft. Maintenance of other supporting equipment: see the respective user manual for the maintenance of various supporting equipment, including motors, electric actuators, instruments, meters, etc. These operating instructions are provided by each supporting manufacturer. The manufacturer will pack these instructions together and provide them to the user