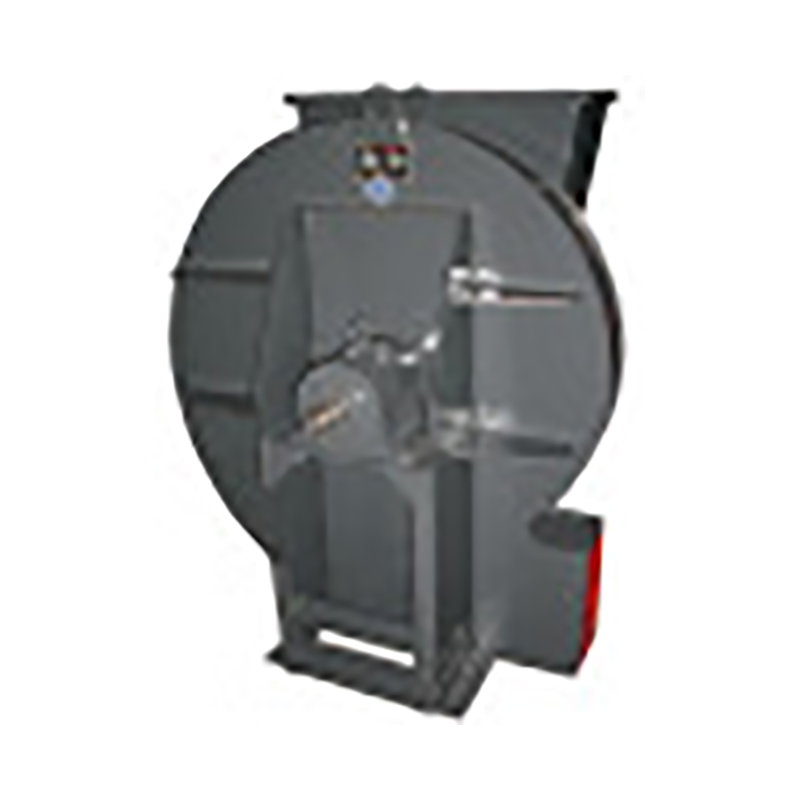
Wet dedusting Price In the use of wet electrostatic precipitator, we will encounter problems of one kind or another. If we do not know how to solve them, we will not know what to do. What are the reasons for the failure of wet electrostatic precipitator? Next, I will analyze it for you. (1) major Wet dedusting The causes of electrical failure include: electrical components are damaged, corona electrode is not adjusted properly, and porcelain bushing and post insulator through the wall are damaged. ① The electrical components are damaged, such as the fuse is blown, the high-voltage silicon rectifier tube is broken down or the thyristor is damaged, which can lead to the power failure; If the milliammeter is damaged or the transformer fails, the phenomenon of fault type (3) will occur. ② If the nickel chromium alloy wire is not used, the corona electrode will be rusted and broken after being used for a short time. The tension of corona wire is uneven, the force is uneven, and the overload of individual corona electrode will also cause the corona electrode to break; If the corona electrode is not installed in place, deviates from the center of the settling tube, or has too much scale, the electric field will flash over frequently, or even the operation will be interrupted. ③ If the mechanical properties of the through wall porcelain bushing and post insulator are not up to standard and cannot bear the tension of the upper and lower hangers, the insulator will be damaged and cracked. The insulator box temperature control is unreasonable, and the temperature is low or changes violently, which will also cause the insulator to be damaged and cracked; Excessive scale on the surface of insulator will also cause damage and crack of insulator. The final result is that the electric field is grounded, the operation of the electrostatic precipitator is interrupted, and faults (2) and (4) occur.
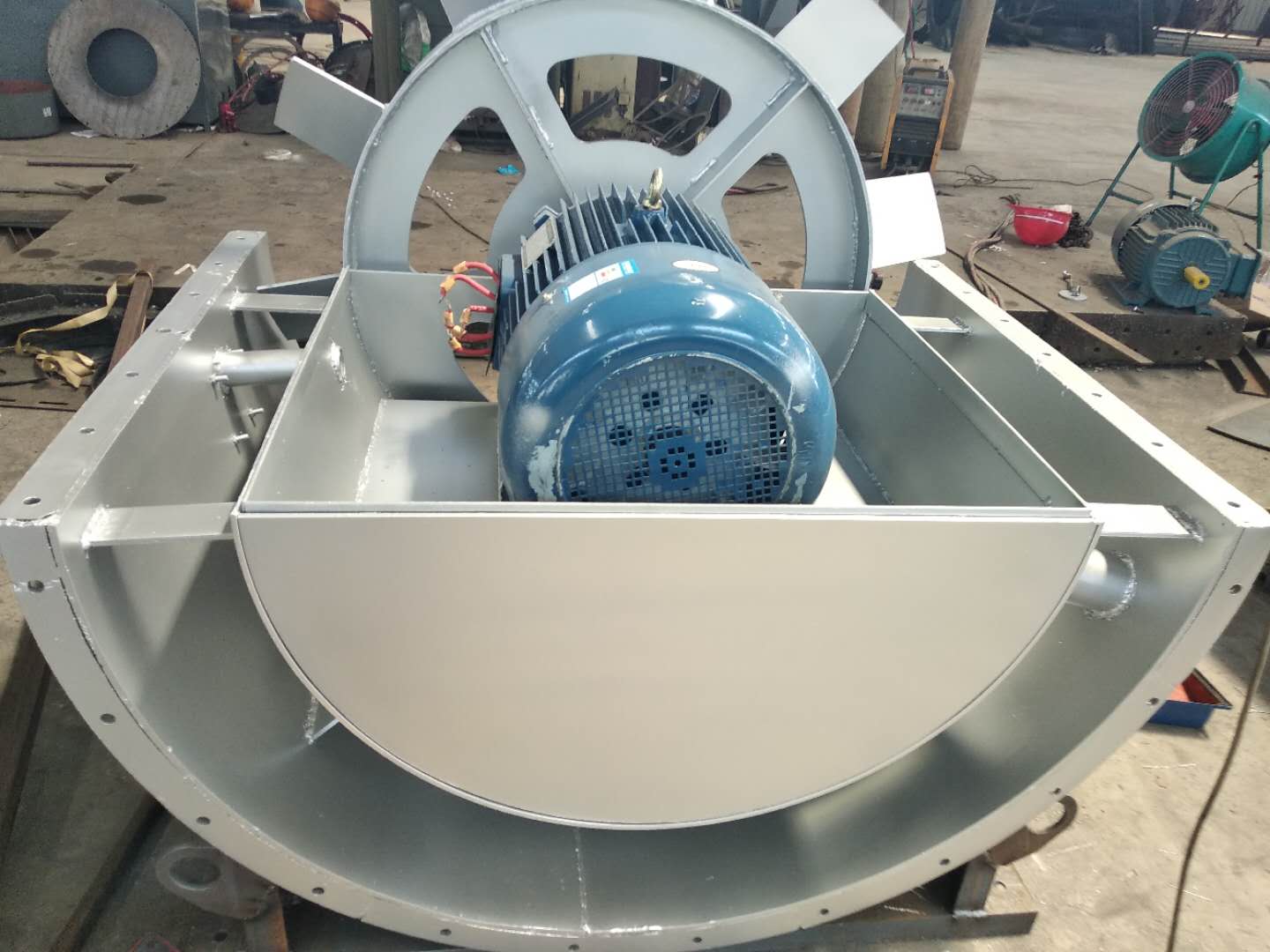
The wet electrostatic precipitator is mainly used to purify water vapor, odor, acid mist and other harmful substances in the exhaust gas discharged by the factory. As an air pollution control equipment, it has also been widely used. let's Wet dedusting Price Understand its system composition together. 1. Composition of wet electrostatic precipitator system. According to its working principle, the control system of wet electrostatic precipitator generally includes high pressure system, water treatment system, low pressure heating and hot air purging system, upper computer system, etc. 2. Design of wet electrostatic precipitator system. (1) major Wet dedusting High voltage system and wet electrostatic precipitator charge the dust through corona discharge of high voltage system. The charged dust reaches the dust collecting plate under the effect of electric field force, and then the dust is removed by regular scouring. (2) Anshun major Wet dedusting Water treatment system. This system deals with the problem of secondary water pollution. It is mainly the water discharged after equipment spraying and flushing, which contains a lot of acid substances and fine particles. Direct discharge will cause secondary pollution. The recycling of water in the equipment consists of two steps: neutralization and acid removal, and separation of suspended solids, so that the sewage can be turned into industrial water suitable for spraying. (3) Heating system. The heating system includes insulator incubator heating, hot air purging heating, and the hot air purging system is composed of fan, butterfly valve and heater. When it starts actively, it starts in the order of fan, butterfly valve and heater. When actively closing, it shall be closed in reverse order. (4) Upper computer system. The selected upper computer system is an industrial control computer, and the network front-end computer is used to enable the system to have extraordinary data acquisition and processing capabilities, so as to meet the requirements of wet electrostatic precipitator for centralized management, decentralized control, energy conservation and emission reduction.
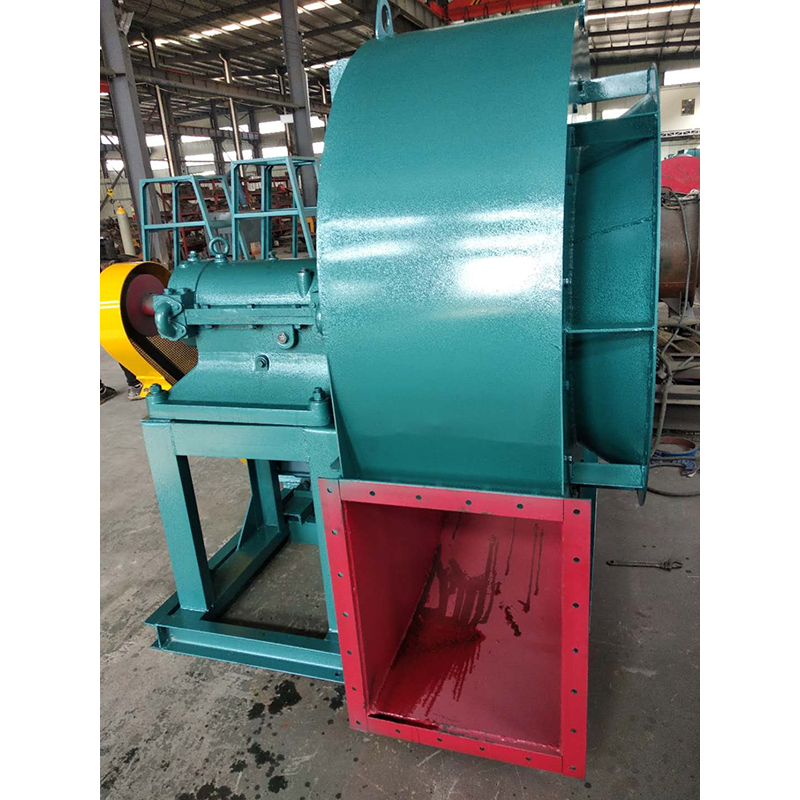
3. When installing Type C and Type B, ensure that the two pulley positions are on the same plane, and the flatness tolerance is 0.5mm. 4. When installing Type D, use a dial indicator and feeler gauge to measure the coaxiality of the fan spindle and motor spindle and the parallelism of both ends of the coupling. The coaxiality tolerance of two shafts is 0.2mm, the parallelism tolerance of both ends of the coupling is 0.2mm, and the spacing between two planes of the coupling is 5 to 8mm. 5. After the fan is installed, move the rotor with hand or lever to check whether it is too tight or collided. The test run can be carried out without overtightening or collision. 6. After the motor is installed, the belt pulley or coupling guard shall be installed. If the air inlet is not connected to the air inlet pipe, the guard net or other safety devices (provided by the user) shall also be provided. 7. Other parts shall be installed according to the corresponding positions in the drawing. 8. Add N46 (ISO VG46, 30) in summer and N32 (ISO VG32, 20) in winter. The oil level should be at 1/2 of the oil window.
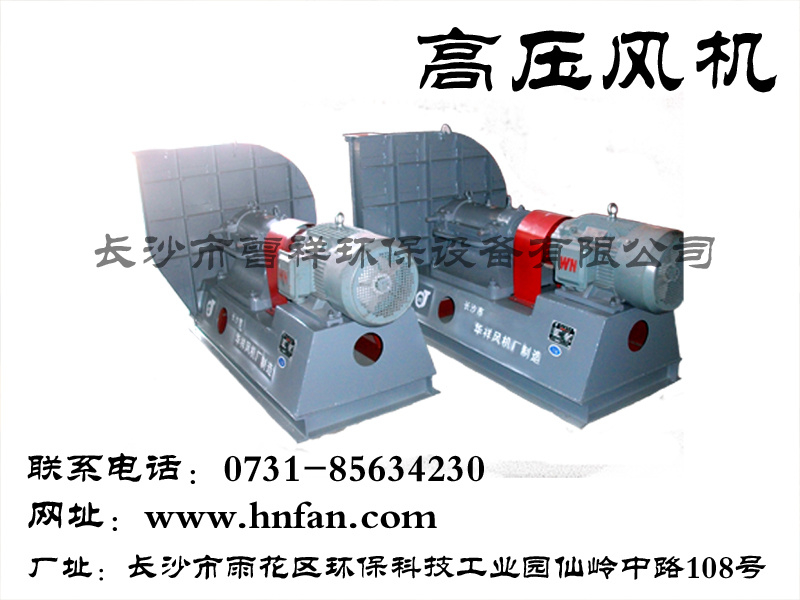
Before installation, first prepare the materials and tools for installation, and check the parts of the fan, especially the impeller, main shaft, bearing and other parts. If any damage is found, repair it, and then clean the inside of the bearing box with kerosene. In the process of installation, the following points must be paid attention to: 1. In order to prevent rust and reduce the difficulty of disassembly, some grease or machine oil should be coated on some joint surfaces. 2. When installing the bolts on the joint surface, if there are positioning pins, install the pins and tighten them before tightening the bolts. 3. Check that there should be no tools and sundries falling or left in the casing and other casings. Installed and used by CHANG factory bridge QIAO ISO9001 quality management system certification enterprise of Beijing No. 2 Blower Works 1. When installing the fan, the inlet and outlet must be provided with soft connection, and the weight of the gas transmission pipeline should not be added to the casing. Correct the gap size between the air inlet and the impeller according to the drawing, and keep the shaft in a horizontal position. 2. When installing the soft connection of the air inlet, the bolts of the air inlet itself can be directly used for connection. At this time, the air inlet is fixed by three countersunk screws.
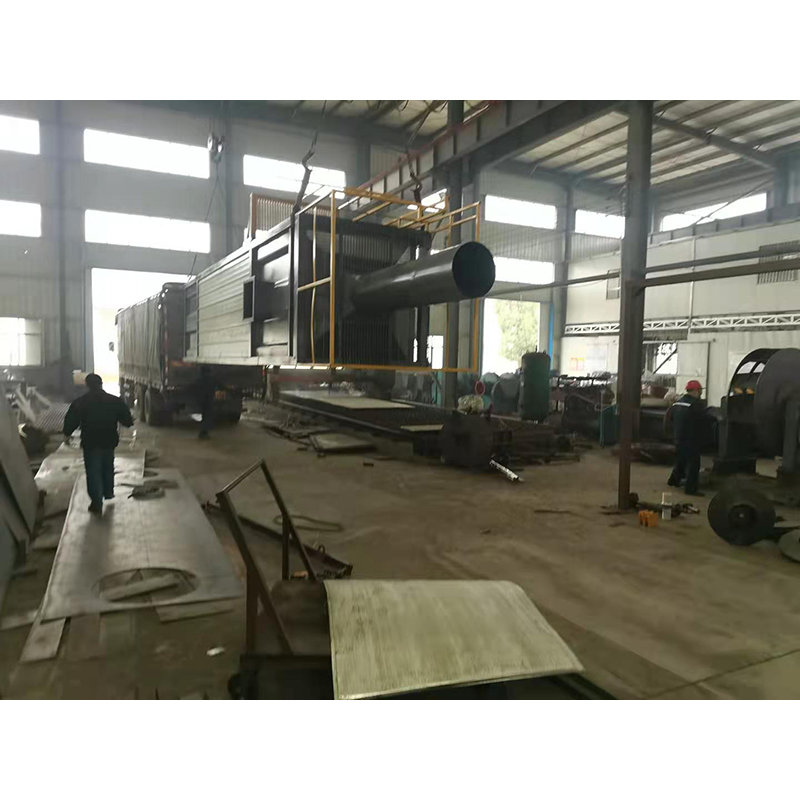
9. Since the flow, total pressure, main shaft speed and shaft power of the fan have a fixed relationship, the main shaft speed should not be changed when the motor capacity does not change. If the main shaft speed increases, the motor may be burned due to overload. The motor power used by the fan refers to the power not required when the air inlet and outlet are fully open in terms of mechanical losses and due reserves under a specific mine. If the outlet or inlet of the fan is not connected to the pipeline or is idle without external resistance, the motor may also be burned out. For safety, a valve shall be added to the outlet or inlet pipeline of the fan, and it shall be closed when starting the motor. After turning, the valve shall be slowly opened until the specified working condition is reached, and attention shall be paid to whether the current of the motor exceeds the specified value. High power motors must be started in proper ways, such as voltage reduction, frequency conversion, etc.
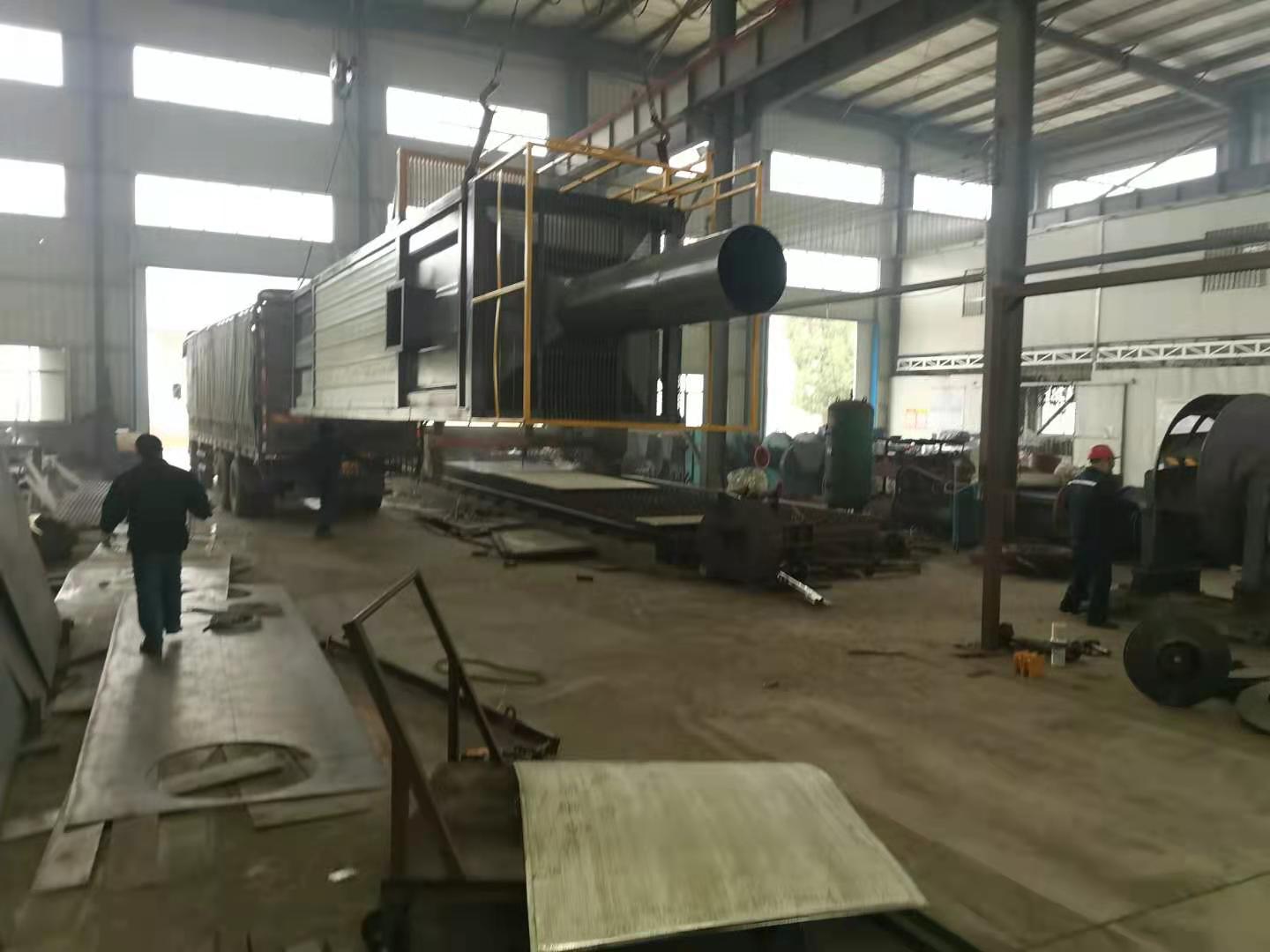
Correct maintenance is an important guarantee for the safe and reliable operation of the fan and the improvement of its service life. Therefore, Wet dedusting Price When using fans, full attention must be paid. Impeller maintenance: at the initial stage of impeller operation and during all regular inspections, whenever there is an opportunity, the impeller must be checked for cracks, wear, dust and other defects. The impeller must be kept clean whenever possible, major Wet dedusting The steel wire brush shall be used regularly to remove the dust and rust on the impeller. As the travel time increases, the dust can not be evenly attached to the impeller, which will cause damage to the balance of the impeller and even cause rotor vibration. As long as the impeller is repaired, it needs to be dynamically balanced again. If possible, the portable trial dynamic balancing instrument can be used for on-site balancing. Before dynamic balancing, check whether all fastening bolts are tightened. Since the impeller has been operating in an unbalanced state for a period of time, these bolts may have become loose. Bearing maintenance: frequently check the oil supply of bearing lubricating oil. If the box leaks oil, tighten the bolts of the end cover a little. If this is not enough, you may have to use new sealing packing. When the bearing lubricating oil is in normal use, it should be replaced at least once every six months. When it is used for the first time, it should be done after 200 hours of operation. The second oil change should be done in 1 to 2 months. After that, the lubricating oil should be checked once a week. If the lubricating oil does not deteriorate, the oil change can be extended to 2 to 4 months. The specified brand of lubricating oil (specified on the general drawing) must be used when replacing, The old oil in the oil tank shall be completely drained and cleaned before new oil can be filled. If the fan bearing needs to be replaced, pay attention to the following matters: before installing the new bearing, the bearing and bearing box must be very clean. Place the bearing in the oil with a temperature of about 70~80 ℃ and heat it before installing it on the shaft. Do not force assembly to avoid damaging the shaft. Maintenance of other supporting equipment: see the respective user manual for the maintenance of various supporting equipment, including motors, electric actuators, instruments, meters, etc. These operating instructions are provided by each supporting manufacturer. The manufacturer will pack these instructions together and provide them to the user